Choosing a magneto inductive device is not any easy task at all. Although the technology has more than 60 years of technical maturity, there are few information available and most of them are not particularly objective. A Magnetic Rope Test (MRT), to be a reliable inspection, necessities of a device designed in a proper way and a correct user’s interpretation.
In this article, we will try to explain through a 8 points analysis what means “designed in a proper way”
1. Certifications
Certificates are a good and immediate tool to understand the reliability of the magneto-inductive device manufacturer. Below we have listed those certificates that turn out to be fundamental for a quality understanding.
- The CE certification is mandatory to sell the MRT device in the European Market, and it shows that the manufacturers has performed and achieved all the necessary tests to satisfy the regulation safety requirements.
- The EN12927-8 certification is mandatory in the Ropeways environment and it is claimed by the new ISO4309:2017 in the Heavy Lifting Sector for the qualification of MRT devices [the guidance should be taken from the EN12927-8 or equivalent (i.e. ASTM E1571)]. To achieve this certificate, the MRT equipment (measuring head and acquisition system) must pass a special accuracy test. The measuring head must find a special inner defect in the inner core of the test-rope and the acquisition system must provide a well-defined signal as output (ratio signal to noise > 2). If an MRT device pass The EN12927-8 certification test, it can detect inner defects.
2. Technology
An MRT device works with magnetic fields and it is properly designed in order to force a strong magnetic field inside the rope, saturating it. The magnetic characteristic of a metallic wire rope is not linear, the correct operative point, the 'knee' of the characteristic, is reached around 2T of magnetic induction. At this point the magnetic permeability of the rope is enough low to ensure that the magnetic field is distributed along all the metallic section, and it is higher than the magnetic permeability of the air, in this way defects can be easily recognized.
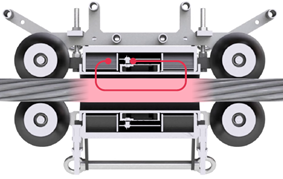
In presence a defect, a part of the flux lines comes out of the rope. These lines are detected by sensors placed in the central part of the device. This signal is called “LF signal”, where LF stands for Localized Faults. A localized defect can be one or more broken wires, but also corrosion or wearing.
Another interesting signal is the LMA. In presence of a big defect, the magnetic flux flowing inside the rope changes. This happens when the rope magnetic reluctance has been modified. This variation in terms of field intensity is detected by probes and it is called LMA, which stands for Loss of Metallic Area. Note that this acronym is not correct. A modification of the reluctance provides us an idea of the metallic volume, not of the metallic area. The correct acronym should be LMV (Loss of Metallic Volume).
Under certain specific conditions (normally if the defect is enough long) it is possible to mathematically compute the rope section variation.
It is important to highlight that same rope section variations have different meanings depending on the rope length. For example, a variation of 5% on a certain length (L) provides a different LMA signal than the same variation on a shorter length. This is normally true if the length of the defect (L) is lower than a minimum value, that should be declared.
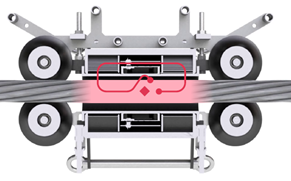
Although working principles are well known, the main difficulty is working at the correct magnetic point, considering vibrations that occurs when the rope is running, and a correct signal filtering.
In our case, all the devices are engineered by using Finite Elements codes to build since the beginning a first virtual prototype. This gives us a correct view of the magnetic behaviour.
3. High magnetic field or not?
Yes! The system must work on the knee of the magnetic characteristic of the rope so the magnetic field must be high. This configuration allows the device to inspect the inner part of the rope.
Low magnetic field provides a different solution. When a rope is not fully saturated, the magnetic field is not uniformly distributed and does not penetrate deeply. In the following pictures it is possible to observe two different Finite Element simulations.
In the first a high magnetic field is applied. The field intensity is uniformly distributed along the rope radius. In the chart on the right, the value of B[T] is plotted.
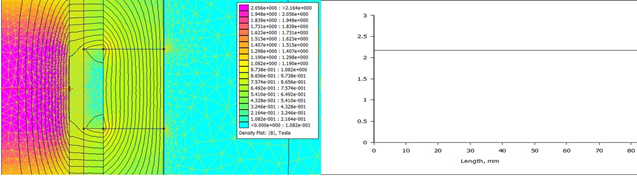
In the second picture, the simulation has been performed by using low fields. The field intensity B[T] is very low in the core of the rope and then increases along the radius.
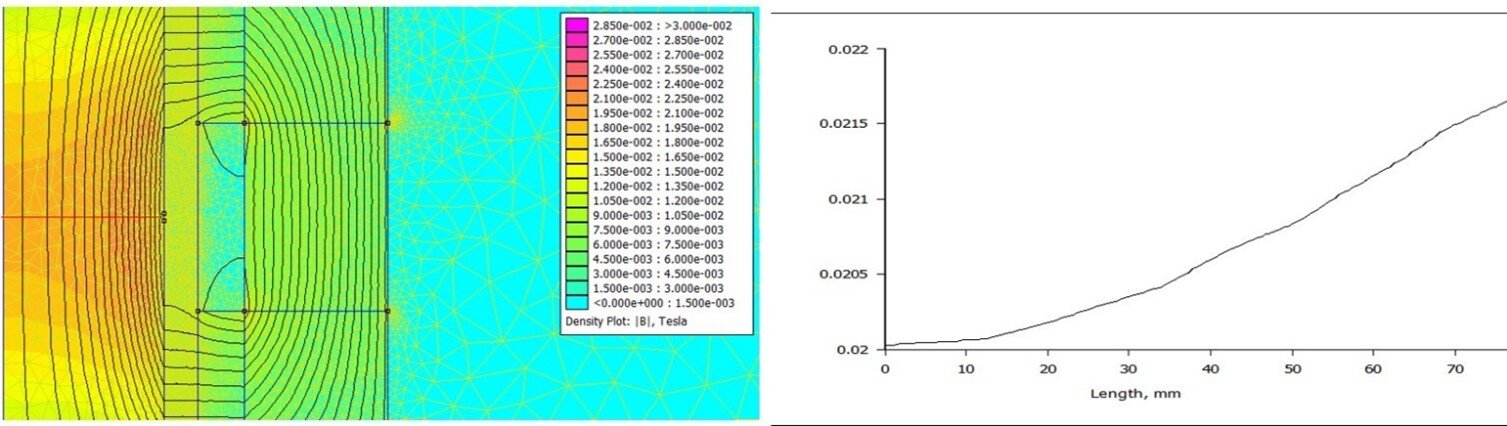
This method is not indicated for inner defects because the magnetic field does not penetrate enough in the rope core. On the other hand, the LF signal is very good for external defects because the low field intensity corresponds to a point in the magnetic characteristic of the rope where the permeability is very high.
In conclusion, pay attention to who propose you low field devices without operative limits in terms of diameters.
4. Coils or Hall effect sensors? The measuring chain
There are different methods for measuring the magnetic field variations. The mostly used ones in MRT are Coils and Hall effect sensors.
The Hall Effect sensors are able to supply a voltage proportional (in a certain range) to the magnetic induction received. The voltage mirrors the magnetic induction in the rope and its variations (defects).
This signal is not theoretically correlated to the speed of the rope inside the device. This probes needs power supply to operate.
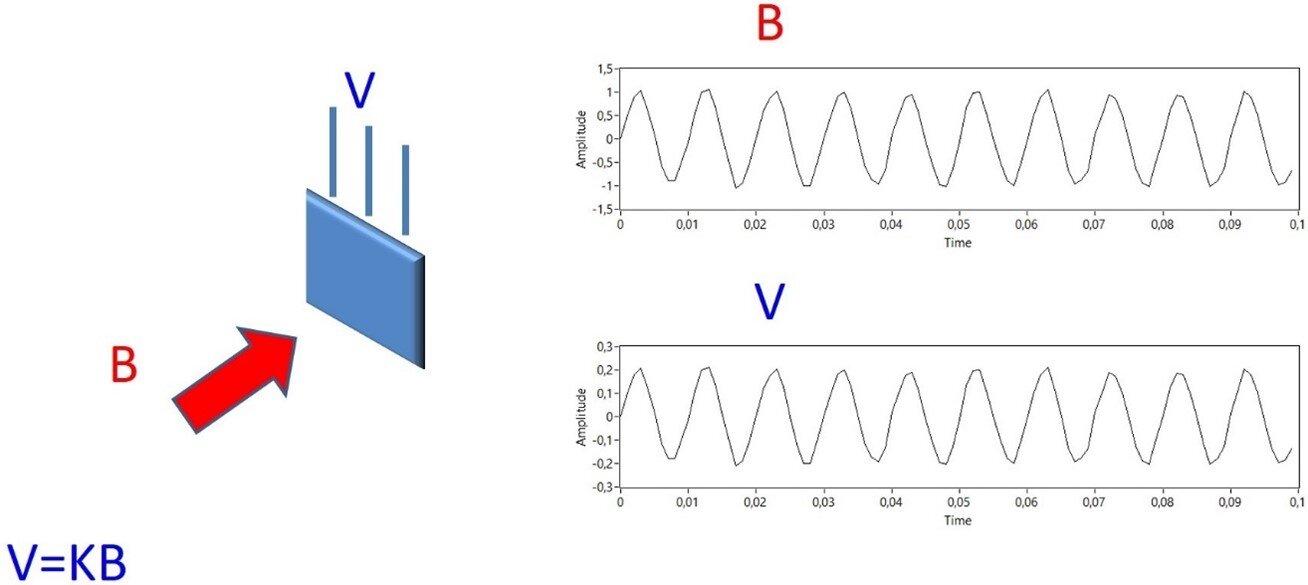
Coils are the 'oldest' sensors used for this kind of inspection. At the terminations of a coil immersed in a variable magnetic field, is possible to measure a voltage which is proportional to the field variation (Faraday law). In this case a voltage mirrors the derivative of the magnetica field and its variations (defects). This signal is proportional to the speed of the rope. If a test is performed at 1 m/s, the relative signal will double the which ones performed at 0.5 m/s. Although if the software can correct this effect, it is important to remember the correlation speed-coil.
Coils or Hall sensors are usually a manufacturer choice.
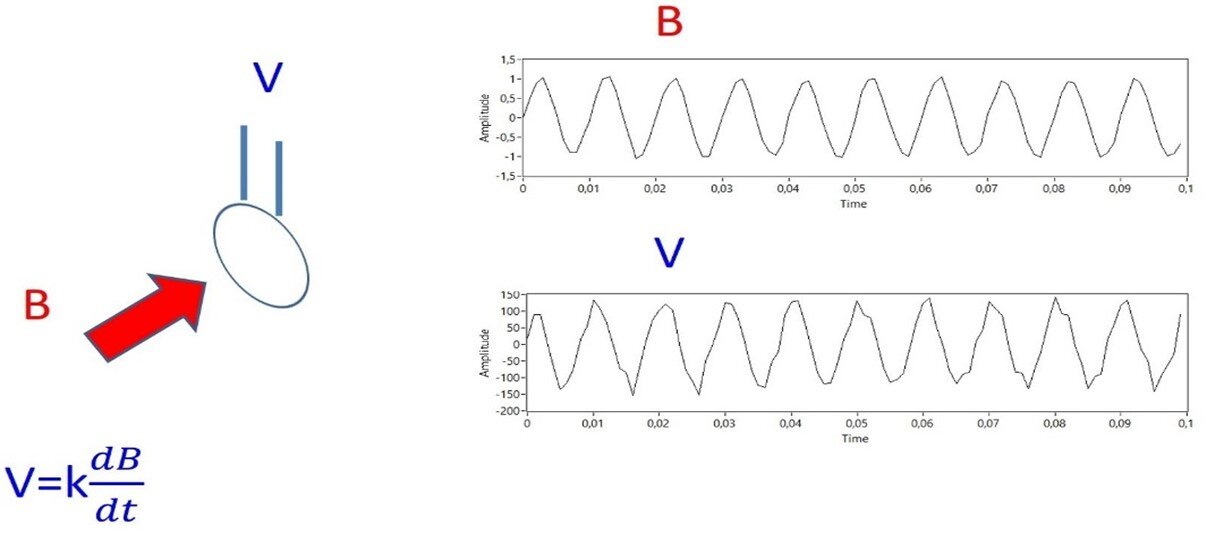
5. Filtering
The output signal is the sum of different frequencies which constitute the rope information. The graph waveform should be correctly managed to maximize the SNR (signal to noise ratio), highlighting peaks and other non-uniformities. The first step is to apply a correct filter.
Using an appropriate filter requires experience. A wrong utilization can lead to a wrong interpretation of the status of the rope. For this reason, the user must be conscious of the difference between an high pass, low pass and band pass filter and he must know what happens to the signal after the use of these filters. The AMC software is presetted with optimized filters value.
Here below some example of the same date filtered in different way.
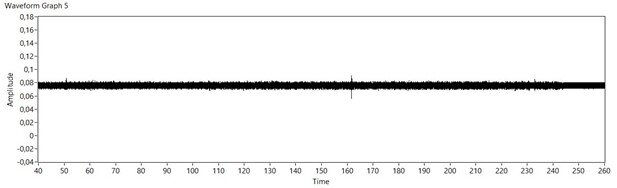
Raw trace obtained on a 20mm rope. The speed of the test was 0.3 m/s and the sample rate was 2500 samples/sec.
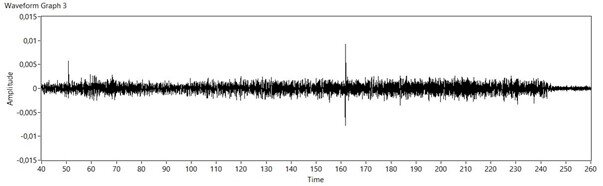
Band pass filter applied, with a low frequency of 1 Hz and an high frequency of 30 Hz. The signal is now certainly better from the point of view of the peaks identification and the noise here is representative of the rope conditions, without external contributions.
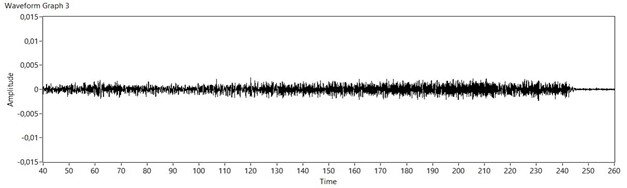
Here the same signal that we analysed before, with a cut at 10Hz.
It is possible to observe that all the peaks disappeared. The signal is wrong, but the user can not know it and consequently the rope is considered in a good condition. This is the reason why the user must be trained for using filters and the software should provide also a raw signal to the operator.
6. Weights and dimensions
There is a strong correlation between the weight and the efficiency of an MRT device, because MRT systems are made of iron and magnets. Systems are built around a specific range of inspection, around the “knee” point and around a desired manoeuvrability. It is better to operate with a small device of 7 kg on a 20 mm rope, than with a 30 kg device.
Of course, also for costly reason, sometimes it is preferred to have a bigger device covering different range. In that case, Bushings & Reduction kit, Centering systems are mandatory to maintain the sensitivity of the equipment.
7. Training & aftersales support
This is probably one of the most important steps. Becoming an MRT inspector requires a rope’s life cycle management. Training & Aftersales support must be part of a path to acquire this specific skill. Training will put the customers in the right working position, learning how to use the device, interpreting the data, using the software and building a report in compliance with the regulation. The Aftersales support will connect the customer with the Service Team in case there is a necessity/doubt/clarification. Training & Aftersales Support After are necessary steps to have a good control of the system, for operate independently with good confidence.
8. Tips & conclusions
Magneto inductive devices are experiential goods. It is not an easy task to choose them, especially for the first time. If you are not far from your supplier, ask always for a comparison demo/test on the field.
Please consider that device is not a “magic tool”, it works under some physical principles for on-field tests (much different from laboratory). Contextualizing the specs of each device will help you in understanding its reliability during an inspection. Searching for a device able to detect the 0.0001% of the loss in section could be useless, whilst do not trust devices without the EN12927 certification (regulated accuracy test). Noting also the correlation between the operative speed and the sampling rate. If the speed range is 0-15 m/s and the sampling rate is 2000 samples/s, it is obvious that there is something wrong. At 15m/s you will be able to collect 2000 points, one point per 7.5mm. It will be impossible to detect fatigue broken wires, which have a typical damaged zone of a few millimetres
Finally, price is important, and it must be aligned with this 8 suggestions points, otherwise the risk of buying something which does not perfectly work is high.
More about Magnetic Rope Testing?
Discover our articles about Magnetic Rope Testing (MRT):
- When is an MRT suggested?
- Rope inspection, safety and the ISO4309 regulation
- The EN12927, is your MRT device in compliance with the standard?
- Localized Fault VS Loss of Metallic Area
- MRT-training
- A permanent MRT system
- The magnetization curve of a steel wire rope
- How is MRT equipment made
- How to develop customized magneto-inductive equipment